Manufacturing logistics is a field where mistakes and delays have severe and resonant consequences.
Parts delays knock production lines down and lose money by the minute.
Regardless of the supply chain environment or state of the economy, the mandate is the same. Precise inventory controls and deliveries are required to ensure the right parts in the right quality are delivered in the right way at the right time.
That’s why supply chains need to be controlled by experienced teams who adhere to streamlined processes and have the ability to respond positively to disruptions.
ODW Logistics handles logistics behind the scenes for some of the biggest and most established automotive and industrial manufacturers in America. We’ve seen major changes over the years and devised hands-on solutions to help customers keep their supply chains rolling reliably and cost effectively throughout the many changes in recent years.
See the leading brands that trust ODW.
Here’s our overview of the top 10 challenges automotive and industrial managers should be most aware of today.
1 – The Rules Have Changed
We’re all facing the realities of the post-pandemic supply chain and the ramifications of the changes that continue to evolve. The biggest of those was the shift from just-in-time (JIT) inventory practices to just-in-case (JIC).
During the supply chain uncertainty of the pandemic, we saw a big buildup of inventory bought JIC. The glut of inventory has driven prices and manufacturers’ margins down. As a result, we’re seeing tightening of the belt and supply chain across every market.
With changes in transportation procurement, a constricted warehouse market and leaps in technology, the variables to effectively cut costs while creating a streamlined supply chain are complex.
Economic decisions have to be balanced with quality and service standards, where the rules remain as high—if not higher—than ever. The price of delays to profitability and customer relationships can be dire and easily wipe out any efficiencies or savings achieved through cost cutting.
Transform your supply chain into a driver of value.
2 – Shifting Focus to Manufacturing Core Competency
Manufacturers who recognize the potential efficiencies and economies in their supply chain are in a bind. The truth is that they usually don’t have a lot of supply chain people on staff who understand the dynamics of driving cost efficiencies in supply chain.
Specifically, manufacturers need to consider how they’ll manage raw material inbound, receive it, catalog it, store it, and then put it in some type of sequence or configuration and deliver it in a kanban or just-in-time manner line side so they can use it.
That’s forcing them to find the knowledge or talent to do so—not so easy in today’s tight labor market. Plus manufacturers don’t want to carry a lot of inventory buffer because warehousing is so expensive today.
As a result, manufacturers are asking if the end result is worth the added cost and effort. Focusing on front- and back-end of the supply chain with its ever-changing learning curve distracts attention from the manufacturing portion of their business that they're experts in.
Find support for your manufacturing operations.
3 – Relinquish Control to Maintain Control
For manufacturers, outsourcing supply chain functions can be an agonizing decision. Maintaining strict controls is the hallmark of manufacturing success. Inserting an outsider into the process can be a psychological barrier.
Manufacturers need tight inventory integrity because when you're dealing with raw materials to line. Counts have to be correct. Otherwise production halts. Also, the quality of the product that arrives to the line has to be at the required standard or the line could go down. To add to the risk, delays snowball and lead to additional costs and end-user dissatisfaction.
On the back end, when a customer orders a finished good, manufacturers need to ensure they have the parts in stock that they say you do. Customers’ operations rely on their ability to receive goods according to their exact timing and specifications.
Maintaining inventory integrity and quality are understandably risky to outsource. Logistics providers who don’t know the risks to production are a liability. So is a do-it-yourself approach to managing carriers and inventory visibility while controlling costs and quality in today’s complex supply chain.
See how ODW's optimized transportation solution helped Plaskolite save $2M annually.
4 – Securing Supply Chain Talent Isn’t Easy
Manufacturers know the challenges of finding, hiring, training and retaining factory workers today. Adding warehouse workers to the list is a significant and separate undertaking.
The cost of recruiting, and paying wages and benefits is considerable in this competitive environment. Logistics for automotive and industrial manufacturing is a specialized field requiring dedicated training and related costs.
In addition, managing employee levels is challenging because labor needs fluctuate based on changes in supply and demand or seasonality. Having a workforce of full- and part-time workers as well as temps enables a company to flex to supply chain needs.
Manufacturers need a reliable pipeline for labor. Failure to adequately staff lowers productivity. Overstaffing blows up operating costs.
Meet our team and see why partnering with us makes the difference.
5 – Prepare to Automate
Given today’s labor crunch, automated warehouse solutions that decrease reliance on human labor are essential.
The risk to continuous production is too great to rely exclusively on human workers. Automation evens out capacity and removes performance variability. Robotic arms, conveyance, carousels and cobots are becoming more and more common in warehouses.
These capital investments can take years to pay off, but to compete, companies must make the leap. Today’s labor crunch only promises to become tighter in coming years.
Companies familiar with manufacturing automation shouldn’t assume warehouse automation processes to be the same. This can be an added challenge to manufacturers who should seek expert counsel before making the leap and automating supply chain processes.
Find automation solutions that increase labor productivity and decrease risk.
6 – Data Drives Efficient Manufacturing Logistics
Tight controls and precise timing define automotive and industrial manufacturing logistics.
The nature of the work has always been challenging, but today’s pace of change and performance demands require data-driven processes. Manufacturers need the means for data collection—often for multiple divisions with separate and distinct needs.
Data regarding inventory levels, lead times and more are like high octane fuel for systems and processes.
Having good data and the means for collecting it are essential. Having the experience to use data to drive change is equally essential.
See how data integration improves supply chain performance.
7 – Made-in-U.S.A. Makes for New Challenges
Over the last five years there's been a big push to have more arm's length control of materials from raw to finished. It’s largely because of the push by the federal government to reshore or nearshore and reduce supply chain risks made obvious during the pandemic.
Moving manufacturing or creating smaller supplier networks within regions has come back. We’re seeing more manufacturing shift from Asia to Mexico, and even back into the United States. This has brought opportunities for increased control as well as the challenge of increased costs related to labor, warehousing and more.
Companies stepping out of supply chains they’re comfortable with need to look at their operations anew. They need to understand the dynamics of driving cost efficiencies in every function of the supply chain—individually and collectively.
Essentials of Integrated Manufacturing Supply Chain
- Inbound delivery through a vendor-managed inventory system
- Inventory management providing visibility and performing identifications, sequencing and QA
- Just-in-time delivery to line-side to meet production demands
- Line-side delivery through a kanban system to keep production lines flowing
- Packaging and labeling for order fulfillment
- Transportation management to final customer
Creating supply chains that run smoothly and efficiently hinges on end-to-end integration of all these functions.
Save 20–30% with ODW's integrated logistics solutions.
8 – Beware of Freight Waste
Optimizing freight is a tremendous opportunity for most manufacturers. It is estimated that 40% of trucks are shipped with empty and available space. Each of those is an opportunity to drive greater efficiency and cost savings.
Freight optimization and potential opportunities for consolidation should be a key focus of any automotive or industrial manufacturer’s transportation management solution.
Manufacturers combatting shrinking margins and facing increasing competition can’t afford to overlook this opportunity to reduce supply chain costs, and as is often the case, improve service to customers.
9 – Manufacturing Logistics Requires Specialized Experience
Automotive supply chain professionals are a rare breed. Many have spent their careers working for automotive manufacturers or Tier 1 or 2 suppliers. Their experience of the supply chain processes that are germane to automotive logistics is invaluable to inventory integrity.
Inventory integrity means having the right quantity of product in the right form to the line at the right time in the right vessel in which it’s needed.
This is absolutely critical when it comes to managing logistics for automotive and industrial manufacturers. Running a production line down can cost $10,000 an hour or more in some cases. Having proven rigid processes and a system that can support the management of the inventory controls are especially important.
Being able to foster that not only through a system, but also through all of the leaders and floor level associates that manage inventory is key. Manufacturers need to make sure the team understands their role and responsibility in ensuring inventory integrity.
See why you get more from your 3PL with ODW Logistics.
10 – Increased Agility and Resilience Required
Today’s omnichannel environment has created expectations in the B2B realm for delivery speed, visibility and flawless fulfillment.
Just like B2C companies, automotive and industrial manufacturers must meet aggressive service level agreements, pivot amidst disruption and scale quickly to meet demand—all while maintaining focus on customer satisfaction.
Manufacturers need to perform to the highest standards without excuses. That means building agile resources for storing, transporting, managing and fulfilling. If you’re not willing to invest in the resources and commit to a resilient supply chain, it won’t matter how good your manufacturing operations are.
Those are the stakes today.
Is Your Supply Chain Optimized for Speed, Economy and Reliability?
What can a manufacturer do if they aren’t prepared to go all-in to create and maintain a world-class supply chain themselves? Third party logistics (3PL) providers were made for this moment in history.
Learn how working with a 3PL enables you to just focus on driving manufacturing excellence by reading our next blog— or reach out to talk to a supply chain expert at ODW Logistics.
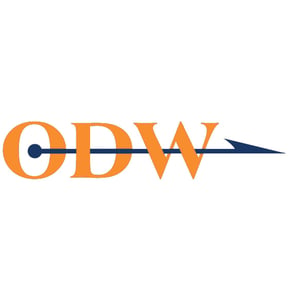
ODW Logistics
Since 1971, we’ve been providing warehousing, distribution, and transportation solutions for hundreds of brands. We operate as an extension of your business to control costs throughout your supply chain that deliver you a competitive advantage over your competition.RECENT POSTS
Streamlining Your Supply Chain for Maximum Efficiency Navigating the Complexities of Modern Grocery Retail The supply ch...
Dec. 03, 2024 09:13 AM
ODW Logistics is expanding its Columbus operations with a newly designed, state-of-the-art distribution campus. This adv...
Nov. 26, 2024 09:41 AM
Columbus, Ohio—2024 — Food Logistics, the only publication exclusively dedicated to covering the movement of product thr...
Oct. 21, 2024 10:52 AM