Warehousing and distribution can make or break your business behind the scenes. If you’re in e-commerce, the stakes are higher and the pace is faster as you battle the many competitors all searching for that extra edge just like you are.
The right warehouse fulfillment services provider will take your operations to the next level and enable you to scale. The wrong one will hold you back, and while the details may seem minor, the headaches can be major. The right provider makes your customers happy. The wrong one leaves them frustrated. The right provider upholds your brand. The wrong one damages it. Given the dichotomy, it’s crucial to be deliberate, inquisitive, and even methodical when selecting a warehouse fulfillment provider. Follow these tips en route to the right choice:
1. Make a Game Plan
There are countless options, including hundreds of third-party logistics providers (3PLs), offering warehouse fulfillment services. How do you even begin to sift through them? Many companies are looking for 3PLs to take the weight of warehousing operations off their shoulders, so a great place to start is to evaluate whether a 3PL like ODW Logistics is the solution you’re seeking. There are a few telltale signs that it might be time to outsource warehousing or make the switch from your current fulfillment services provider to a 3PL. These include getting ready to scale, a sputtering supply chain, underwhelming performance, or angry customers waiting too long for deliveries.
Choosing to go the 3PL route is just the beginning of the process. Then, it’s time to assemble an internal decision-making team, perhaps hire a supply chain consultant, create a checklist for evaluating 3PL candidates, and begin interviewing 3PLs whether through an RFP or online search. Your decision-making team should include at least one member to represent every department in your organization, from operations, distribution, and transportation to production, finance, quality assurance, IT, and HR. See a detailed checklist to use when exploring and comparing 3PLs.
2. Consider Warehouse Location
Experienced logistics professionals know that certain locations are geographically advantageous for shipping. Sure, we enjoy the modern infrastructure and technology to ship to and from anywhere, but a strategic warehouse location can allow you to ship smarter and faster, resulting in greater efficiency, scalability, and cost savings. One of those strategic warehousing hubs is Ohio, which has become an e-commerce capital thanks to its proximity to the populous Northeast and Midwest regions and access to all modes of transportation cross-country.
Specifically, Columbus, Ohio—home to ODW’s headquarters—is within a 10-hour drive of 46% of the U.S. population. Branching out, it reaches 90% of the U.S. within two days of transportation. “Columbus is a market that has a lot of good attributes in terms of distribution, access, and availability of parcel carriers that offer competitive rates,” said Jeff Clark, ODW’s Executive Vice President. ODW also has warehouses in Toledo, Ohio, Brookville, Ohio, Waukesha, Wisconsin, Chicago, Illinois, Jackson, Tennessee, McDonough, Georgia, Redlands, California, and Ontario, California—collectively covering all of North America.
3. Seek Relevant Expertise
Warehousing and distribution may seem generalized, and there are certainly logistics best practices that apply to any and every industry, but different providers specialize in different verticals. A 3PL with experience in your industry has the knowledge and expertise to deliver a strategic advantage to your supply chain with specific strategies for things like retail compliance measures, storage configurations, pick-and-pack solutions, and regulations.
A 3PL with expertise and experience in your industry can anticipate obstacles, recognize challenges, and provide solutions. They can also help establish realistic benchmarks for success based on what has worked with other similar customers. At ODW, we specialize in providing warehousing, distribution, and logistics for personal care, cosmetics, food and beverage, consumer goods, automotive, and industrial manufacturing. Learn more about our expertise in each of these industries.
Health and beauty products showcase why industry expertise matters. Safety, security, location, e-commerce capabilities, and flexible space are important factors to consider in cosmetics and health and beauty fulfillment. Additionally, they can be more subject to dramatic changes in demand due to things like influencer marketing and popular trends. A 3PL with industry expertise can help you navigate fluctuating demands, allowing you to pivot quickly and scale seamlessly along with upswings and downswings. Health and beauty products can also be expensive, calling for detailed tracking and enhanced security for high-value items.
4. Compile Your Warehousing Operations Data
One of the main benefits of working with a 3PL is that they exist to drive efficiency for your business. The more they can streamline fulfillment, the more they can help you save and grow, which means you can do more business with them. It’s the ongoing chain of success that makes the customer-3PL relationship rewarding for both parties.
In order for your 3PL to show early wins for your business, they need data on where you currently stand. From this data, they will be able to identify opportunities and make recommendations. The data also helps them provide the most accurate and favorable pricing possible. Without data in hand, they will need to price in uncertainty early on.
If you don’t currently have strong data management in place, ask your 3PL to assist with designing a strategy to build data transparency and management. It will take some work upfront, but it will be worth it to secure the best pricing for fulfillment while setting the foundation to build on and measure against.
5. Schedule Warehouse or Distribution Center Walkthroughs
As discussions progress with a handful of providers you like the most, ask your final candidate(s) to provide a tour. They will be glad to show you the scale of their warehousing and fulfillment capabilities, and you will get to see their facilities for yourself first-hand. Meeting in person is a great way to build rapport, and visiting a warehouse is the only way to truly know how efficiently it operates. During a tour, you will pick up on all sorts of things that you don’t get from a phone call or videoconference, like how clean and organized a warehouse may be, what safety policies are in place, and how happy and motivated the warehouse employees are at work.
If you are not able to tour the specific warehouse you are planning to be in, consider scheduling multiple facilities similar to your intended location. During any tour, be sure to ask questions relating to your warehousing needs. It should be as much of a Q&A as it is a show and tell.
6. Vet for Warehouse Technology and Automation
Just like office buildings, warehouses are becoming more technologically advanced. Some 3PLs use artificial intelligence (AI) and automation to build operational efficiency, increase throughput, and drive labor cost savings. It's not necessarily a need-to-have, but automation is much more than a nice-to-have. Whether in hardware, software, machinery, or any combination of the three, warehouse automation can enable greater efficiency and accuracy in operations. It can also enhance both customer and employee satisfaction as well as safety. Read our Essential Guide to Warehouse Automation to understand how it can benefit your supply chain.
Most companies don’t have the time or resources to invest in warehouse automation themselves, so they look to a 3PL with that technology already up and running. Automation is on full display at ODW’s flagship e-commerce fulfillment center in Columbus, Ohio. A Tier 1 warehouse management system (WMS) integrates with automated machinery for product handling, pallet management, conveying, processing, and more. See how our investments in warehouse automation technology set the stage for 50% full-time equivalent (FTE) savings and a 115% increase in hourly throughput for one of our food and beverage customers.
7. Look for a Long-Term Contract Logistics Partner
Contract logistics are best thought of as a partnership between you and your 3PL. Agreements can range from three to five years, but with increasing demand, it’s not uncommon for contracts to approach 10-year agreements. A long-term agreement gives your 3PL a better runway to make big-picture recommendations and align to your strategic goals and objectives to drive maximum efficiency in your supply chain.
If your business is stable and/or scaling quickly, consider leaning into a 3PL’s expertise, relationships, and contract logistics services. Many of our most successful case studies at ODW are with longstanding customers. David Giardino, FitFlop’s Director of North American Operations said, “From top to bottom, ODW makes themselves available to us. We have had the same level of investment from everyone we have dealt with there from the start. And that hasn’t changed over our six-year partnership.” Read the Case Study.
8. Find the Culture Fit
It’s not all about the numbers and contracts. Those aspects are important for doing viable business, but once again, the X factor is the relationship. Finding a 3PL that reflects your company's ethics and culture will make the relationship click almost automatically. What is a given 3PL’s ownership structure? What is their mission? How about their values? Does their culture align with yours? The answers to these questions form the basis of how a 3PL will deliver its services to you and the experience you will have along the way.
9. Confirm Certifications
In line with industry expertise, the right warehousing provider will have the necessary industry certifications to store and handle your products. For example, organic foods have United States Department of Agriculture (USDA) requirements beyond the standard U.S. Food and Drug Administration (FDA) requirements for food storage. An organic-certified warehouse must work to ensure there’s no cross-contamination from non-organic foods, and must also provide enhanced temperature control since organic foods may spoil more quickly. If you’re selling food outside of the U.S., your 3PL will also need to be certified with international agencies such as the British Retail Consortium (BRC) and Canadian Food Inspection Agency (CFIA).
Some warehouse certifications may be required for your product to be compliant, while others show that a provider is going above and beyond to enhance their operations. If you’re unsure of the certification requirements for storing your products, ask candidates during the interview process—yet another opportunity to see if they truly know their stuff. Deeper in the interview process, you might also consider asking a provider if their key team members have any additional certifications that make them uniquely qualified and experienced.
10. Ask the Right Questions
As you’re interviewing warehouse fulfillment providers and 3PLs, you’re going to ask all the basic questions somewhat naturally. Take it to the next level and ask more detailed, uncommon questions. Here are a few examples:
- In your relationships with customers, what value and benefits do you commonly get positive reinforcement on?
- Where do current customers find the greatest value in partnering with you?
- What defines your company and what are your organizational values?
- How are your customers supported from the bottom up?
- What is your customer retention rate?
- What makes you unique from other 3PLs?
- Given your experience in my industry, what value can you deliver to my supply chain?
Rather than receive bids and make a quick pick, it’s better to get to know a provider before you entrust your warehousing and fulfillment to them. After all, you’re essentially putting your business and brand in their hands.
In other words, ask us anything and everything. Grill us on our business structure. Ask us to give examples. Visit our facilities. At ODW, we deliver trust fueled by transparency. Our approach revolves around learning your business and designing the right supply chain solution for you. Learn more about our warehousing and distribution services.
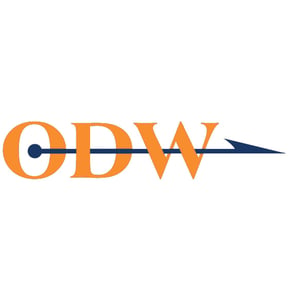
ODW Logistics
Since 1971, we’ve been providing warehousing, distribution, and transportation solutions for hundreds of brands. We operate as an extension of your business to control costs throughout your supply chain that deliver you a competitive advantage over your competition.RECENT POSTS
Streamlining Your Supply Chain for Maximum Efficiency Navigating the Complexities of Modern Grocery Retail The supply ch...
Dec. 03, 2024 09:13 AM
ODW Logistics is expanding its Columbus operations with a newly designed, state-of-the-art distribution campus. This adv...
Nov. 26, 2024 09:41 AM
Columbus, Ohio—2024 — Food Logistics, the only publication exclusively dedicated to covering the movement of product thr...
Oct. 21, 2024 10:52 AM